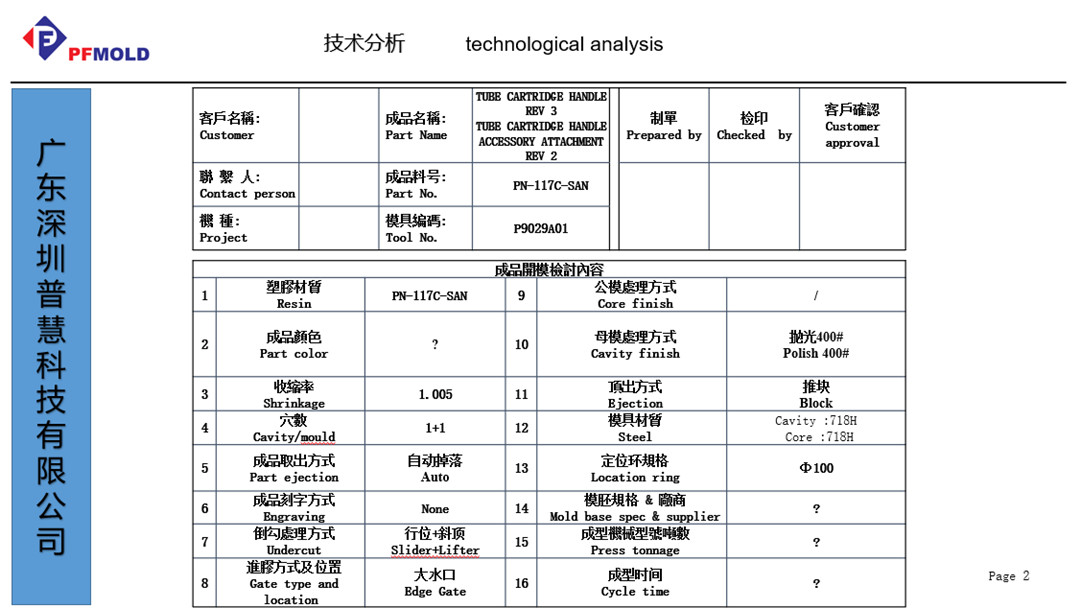
The importance of designing for manufacturing is underlined by the fact that about 70% of manufacturing costs of a product (cost of materials, processing, and assembly) are determined by design
Decisions, so a comprehensive mold manufacturing and part analysis DFM report before official mold design will be the first step to success. As a mold maker, the more potential problems you foresee, the less risk you will have in the manufacturing and parts production processes.
That’s why we always support the DFM report to our customers, no matter whether they asked or not.
There are multiple benefits of the DFM reports:
● Solve the complex problems of wall thickness
● Gate location optimization
● Mold cavities fill consistently and uniformly
● Discover defects in design geometry
● Prevent costly mold errors and rework
● Enhance the manufacturability
● Get faster production to shorten the time to the market
● Boost efficiency and quality
● Reveals potential visual defects, including air traps, sink marks, and weld lines
● Evaluate different material options for pre-production
● Provides data to support design changes
In the meantime, we will also support Mold flow analysis (MFA) reports, When the product's design is more intricate, the flow is less predictable.
We recommend that you work with a seasoned contract manufacturer, one that can guide you through the Design for Manufacturing (DFM) process from start to finish. Find a manufacturing partner who has the know-how and experience to handle the flow analysis for you.
So, if you have a project that has many worries, the Professional PF Mold team can check all of your part drawings and make a DFM report and Moldflow analysis for you, summarize all of the possible issues in the datasheet and send it back to you for approval.
Let’s get started on your successful project!
Post time: Sep-01-2022